Supply chain network risk & resilience
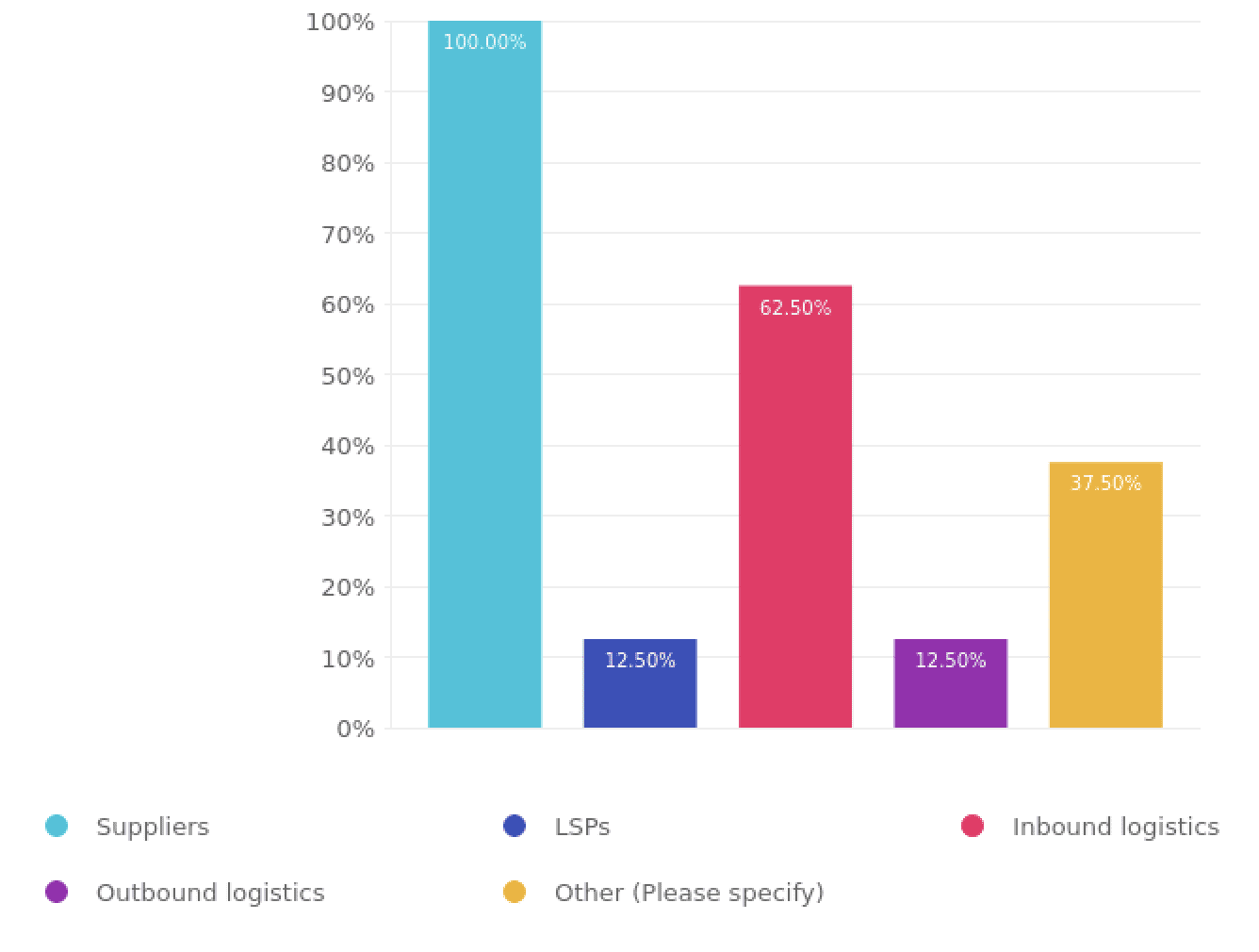
- identifying the risks in the first place as even suppliers rarely know where they are which means getting caught out by substantial disruptions two or three times a week. This is impacting on supplier relationships which feel like they're at an all-time low because of their inability to satisfy requirements;
- even with known risks, visibility is limited or non-existent so that's the focus with suppliers before a second phase to actively start managing the risk;
- using own 3PLs almost on a FOB (Free On Board) basis where there is no payment until the shipment lands as the management of freight and logistics has been so poor, even by some major global manufacturers;
- building inventory for finished goods or components for A-class SKUs to protect revenue;
- setting up a consolidation centre for all demand for a small number of products to reduce the forecast and supply risk before distributing out to business units;
- high variability in shipments from the Far East and even accepting that some of them are now getting lost;
- unpredictable compliance requirements, particularly with China change rules quite drastically with little or no guidance about what to do instead;
- incorporating risk assessments into planning processes, systems and parameters and using technologies that can identify upstream disruption, quantify risks, capacity utilisation and other factors that need to be taken into account;
- a dedicated project to share information with suppliers with the goal of co-planning and scenario modelling to be more prepared for disruptions.
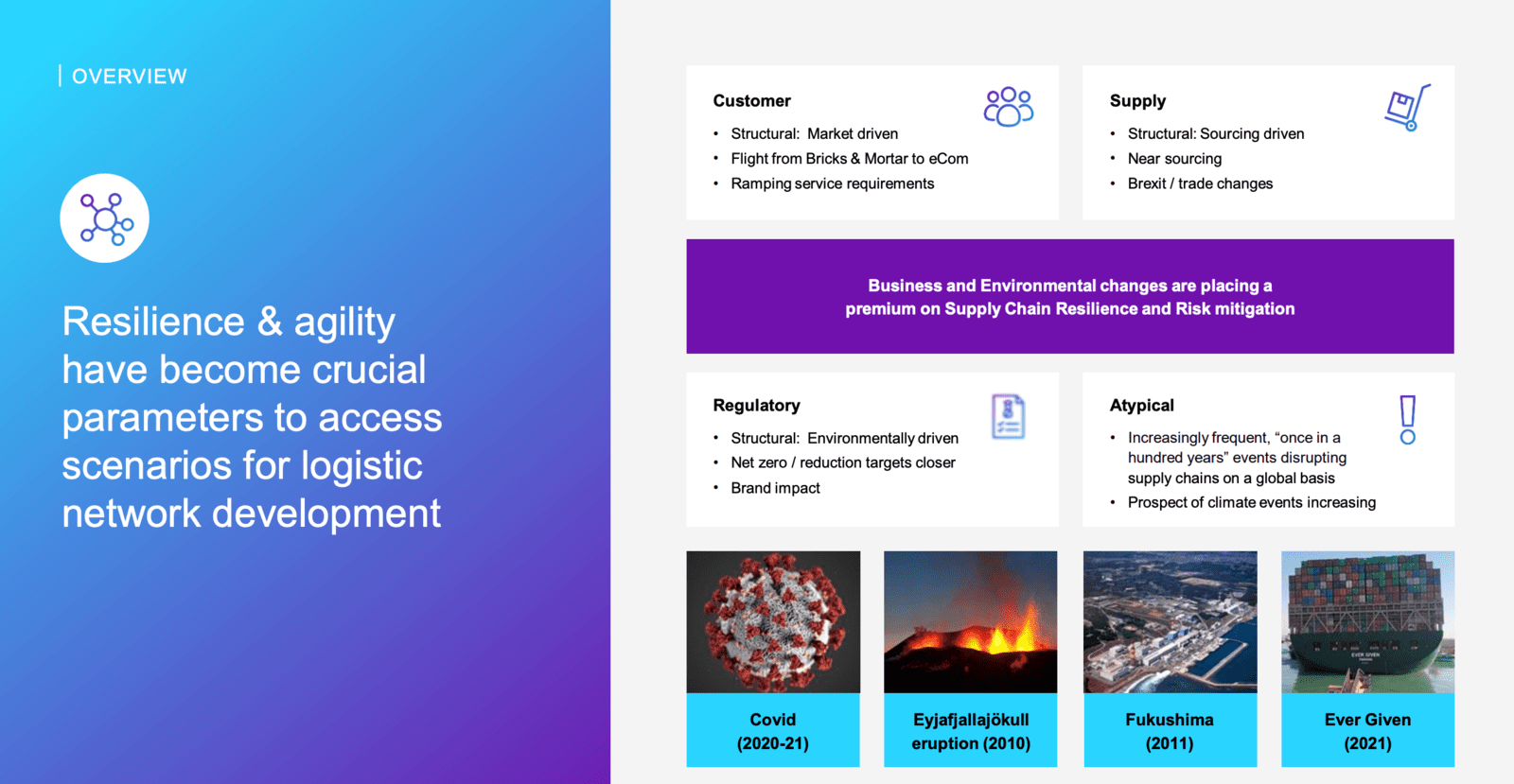
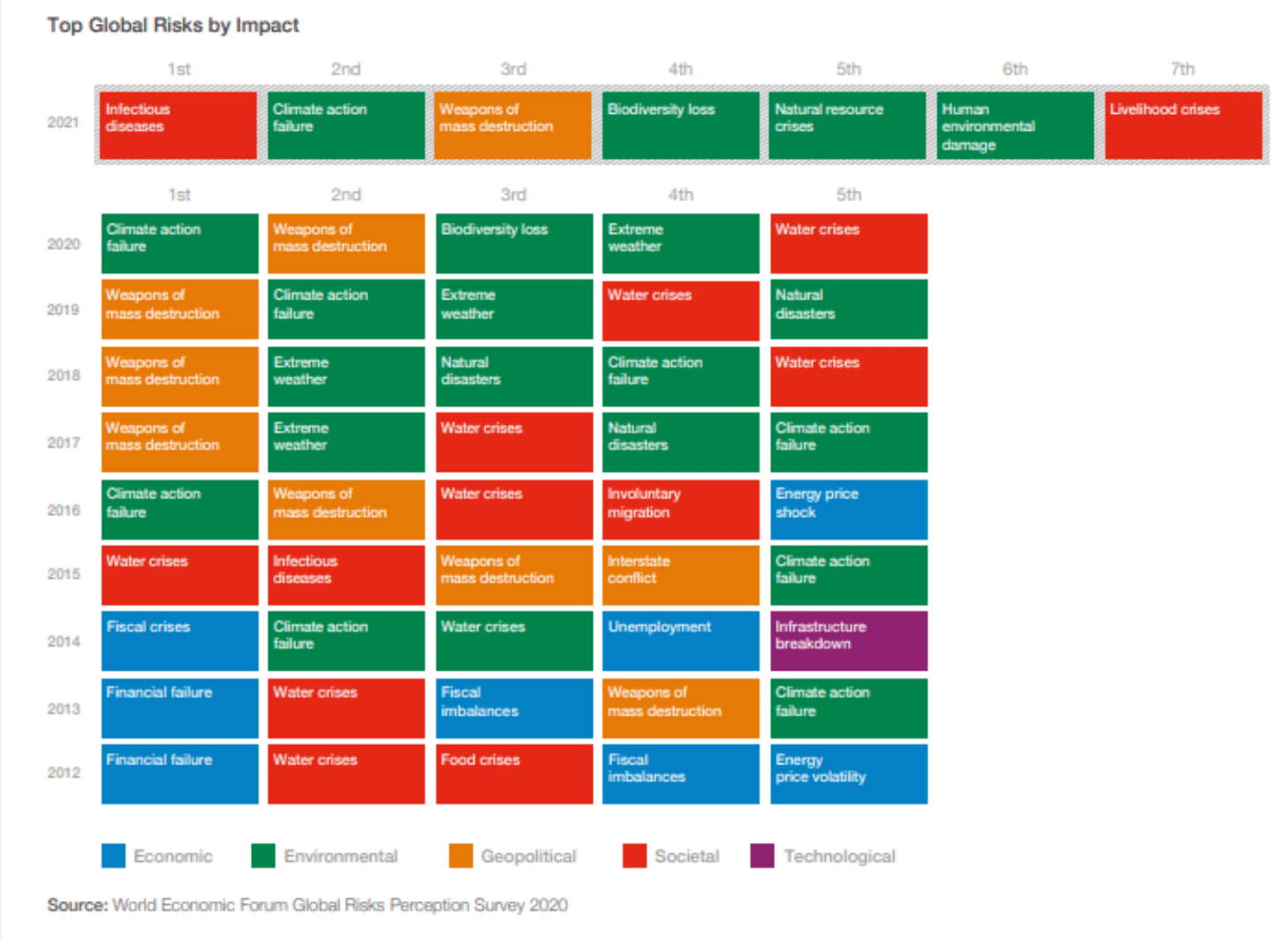
Participant reflections on top global risks:
- in addition to the ongoing labour availability challenges, there has been an increase in staff taking time off due to Covid-19 so there are concerns about how this could play out if the situation deteriorates;
- extreme weather and natural disasters are having an impact on material availability becoming more volatile as well as putting plants out of action for weeks or months;
- the fall-out from the Ukraine conflict in terms of energy availability and cost is increasingly hard to predict;
- inflation seems to be cooling demand as people have less purchasing power or put more into savings. Biases of 38% where before they were +/- 5% are not unusual now;
- not listed in the graphic but the cumulative degradation of supply chain technology was cited as a source of risk which is compounding by the challenge of justifying investments, especially in businesses with narrow margins whose focus is skewed towards tomorrow's performance rather than longer term performance, particularly regarding the resource mix within teams.
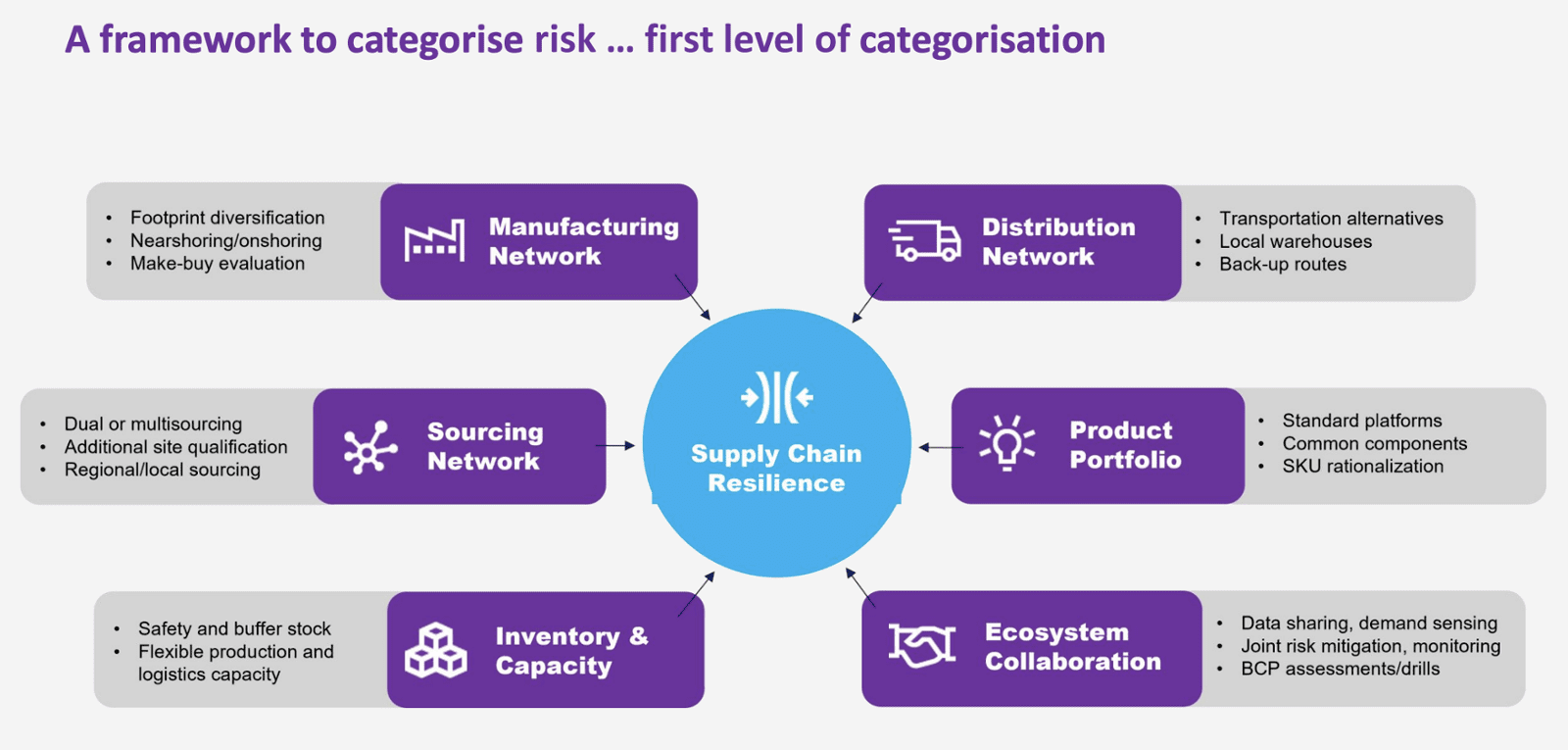
In addition to risk identification, a lot of effort is going into developing risk management frameworks and the concept of a risk management life cycle which also incorporates planning for risks, assessing risks as they emerge through to the mitigation and ongoing surveillance and control. Such frameworks can be helpful to establish a common view and understanding of risks throughout the organisation and with supply partners. A single risk and quality control process also eliminates the noise of different practices being employed in different parts of the business, helps quantify the risks and produce clear and actionable analysis with executive level participation for monitoring and decision-making.
Network scenario modelling tools, often called digital twins, but essentially a quantified and structured set of data is a necessary starting point for managing risk and, therefore, that requires a software platform to use it. The various tools available all have broadly similar capabilities. The real strength of building simulation models is that it helps build business cases with senior management who control the budget because it is possible to show a range of alternative potential strategies and begin to quantify the return on investment of the optimal strategy. For example, it can be very helpful to demonstrate the improvements in service uplift that justify additional costs in the supply chain.
A consistent challenge is getting the granular level data to build simulation models and workarounds like taking a set of dedicated data can make it more difficult to operationalise. It's not uncommon for a 12-week project to spend at least half that time on data collection and validation. That's why it's a good idea to link network scenario modelling with a data warehouse project. Rather than trying to model the entire network of several tiers of supplies, start with a small section which pose major risks and use the learnings from that to generate buy-in from other suppliers over time.
Another major benefit is bills of materials simulation to model inventory levels and either to engage suppliers on specific aspects of performance or to identify strategic inventory to ensure continuity but that requires higher level sign-off to use.
Other use cases include:
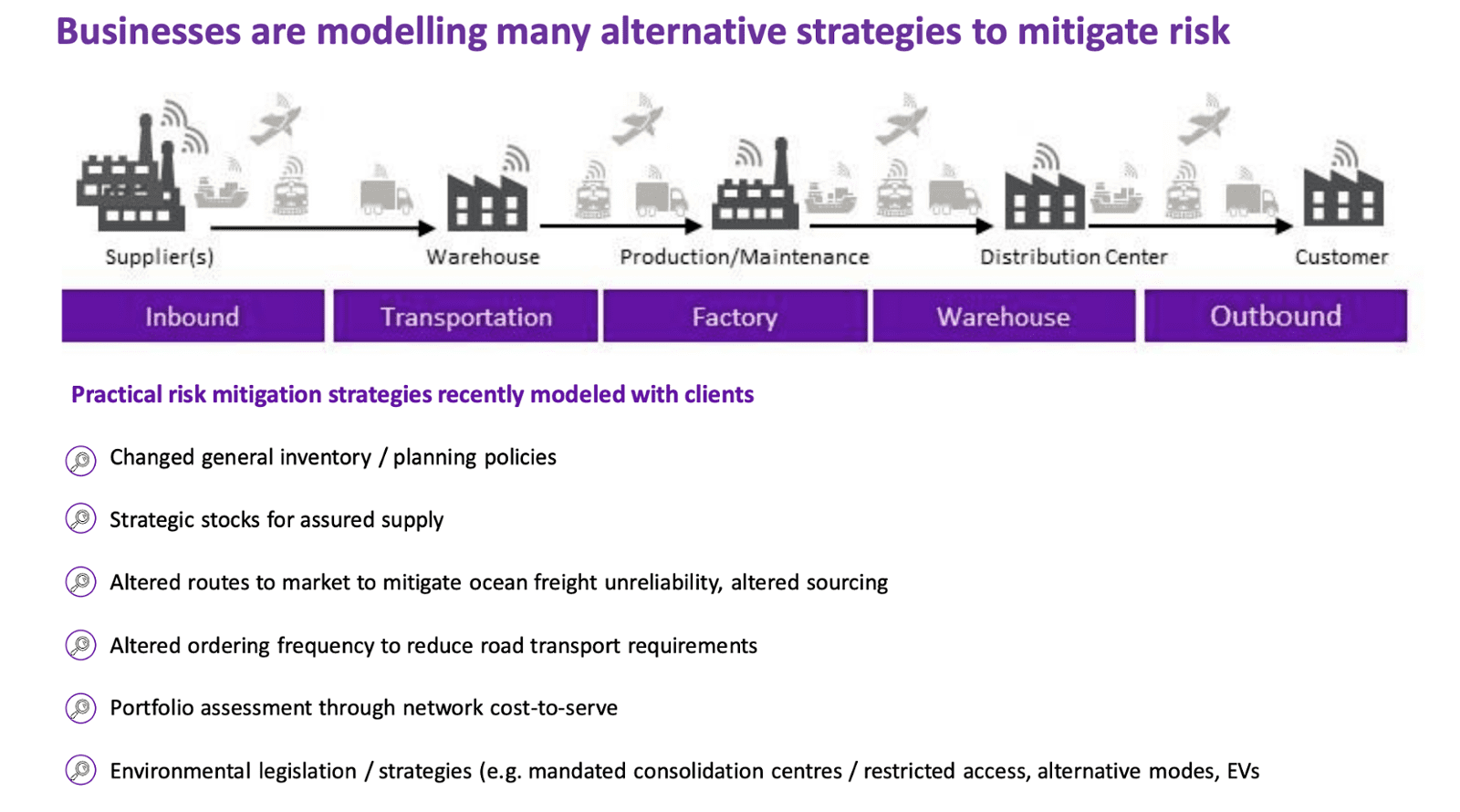
Sign up for monthly updates & session outputs
Tell us which sessions you'd be interested in joining
Top SC Planning Best Practices...Digested
Real lessons learned distilled from a series of practitioner exchanges on...
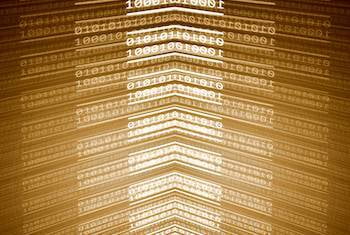
Digital Transformation of Supply Chain Planning
Digital transformation has been on corporate agendas for some time already but, borne of necessity, tangible progress accelerated significantly since 2020. A silver lining of the pandemic may be that the business case is clearer so the focus has shifted towards implementing and scaling digitalisation initiatives.
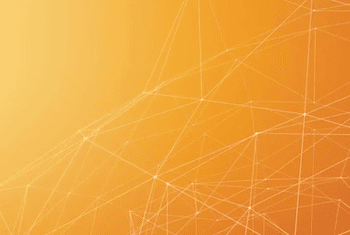
Supply Chain Design Modelling and Analytics
Supply chain network (re)design used to come around every few years or so, often based on quite a high level view of customer segments and associated costs. Now, competitiveness and even business continuity relies on the capability to dynamically adapt network flows based on a much more granular understanding of cost drivers.
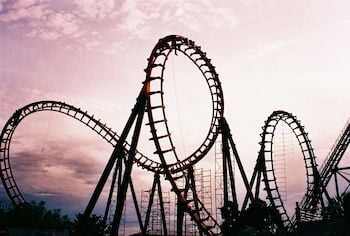
Volatility, Agility & Resilience: Next-Level Planning
Volatility, Agility & Resilience: Next-Level Planning
Volatility, uncertainty, complexity and ambiguity was already an increasing factor before the pandemic but, now, it is clear that we need the next level of demand forecasting, sensing, planning and execution.